What is HDT?
The Heat Deflection Temperature (HDT), or Heat Distortion Temperature, is a measure of a polymer’s resistance to alteration under a given load at an elevated temperature. It is also known as the ‘deflection temperature under load’ (DTUL) or ‘heat deflection temperature under load (HDTUL)’. Basically, it tests the stiffness of a material as the temperature increases.
It is the temperature at which a polymer test bar will be bent at 0.25 mm under a given weight. It is one of the two basic test methods for assigning a value to the performance of a plastic at high temperature. The 0.25mm value is arbitrary and does not have any significant meaning.
Why is HDT significant?
As with any machined part, during the design phase, it is critical for a machinist to know how a material will react to heat produced while machining occurs. Tools produce heat when they come in contact with materials and plastics have a tendency to move with heat. In order to get a finished product with the right dimensions and tolerances, it is important to understand the heat deflection temperature of a given polymer.
Other reasons include:
- HDT represents a value which can be used to compare different materials with each other
- It is applied in product design, engineering and manufacture of products using thermoplastic components
- A higher HDT temperature means a faster molding process in injection molding processes
Tests to Measure Heat Deflection Temperatures of Plastics
The American Society for Testing and Materials, or ASTM, standard for measuring HDT is called ASTM D 648; this standard is equivalent to the ISO 75.
The two common loads used in heat deflection testing are:
- 0.46 MPa (67 psi) – this load is usually for softer grades of plastic like polyethylene (PE) or LDPE.
- 1.8 MPa (264 psi) – this load is used for more durable grades of plastic like PEEK or polycarbonate (PC).
There are tests performed at higher loads such as 5.0 MPa (725 psi) or 8.0 MPa (1160 psi), but we won’t discuss them in this brief.
Limitations that are associated with the determination of the HDT is that the sample is not thermally isotropic and, in thick samples in particular, will contain a temperature gradient.
During the ASTM D 648 test, a testing rod made of the selected polymer is placed on an apparatus like the one in the diagram below.
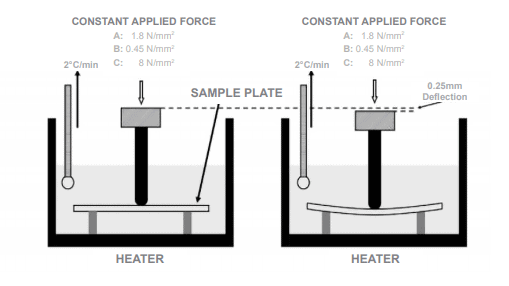
The bar is molded a specific thickness and width. The sample is then submerged in oil while the temperature incrementally increases (usually about 2 oC per minute). The constant applied force, or load, is pressed to the midpoint of the test bar. The temperature at which a bar of material is deformed 0.25mm is recorded as the HDT.
HDT at 1.8 Mpa (264 psi) Values for Common Polymers
Polymer Name | Min Value (o C) | Max Value (o C) |
ABS – Acrylonitrile butadiene styrene | 88 | 100 |
PA – Nylon Polyamide, 66 30% Glass Fiber | 230 | 255 |
PAI – Polyamide-Imides (TORLON) | 275 | 280 |
PBI – Polybenzimidazole (CELAZOLE) | – | 426.6 |
PC – Polycarbonate, high heat | 140 | 180 |
PE – Polyethylene, 30% glass fiber | 121 | 121 |
PEEK – Polyetheretherketone | 150 | 160 |
PEI – Polyetherimide (ULTEM) | 190 | 200 |
PP – Polypropylene (30-40% Glass fiber-reinforced) | 125 | 140 |
PP – Polypropylene Homopolymer/Copolymer | 50 | 60 |
PS – Polystyrene, high heat | 85 | 100 |
PSU – Polysulfone | 160 | 174 |
PTFE – Polytetrafluorethylene | 45 | 50 |
PVC – Polyvinyl chloride, rigid | 54 | 75 |
PVDF – Polyvinylidene fluoride (KYNAR) | 50 | 125 |
Factors That Influence HDT
The HDT gives a short-term performance under load at elevated temperatures for a polymer by measuring the effect of temperature on stiffness. Yet, this is only an estimate and should not be used to predict how the final part or component will perform.
Other factors will significantly influence the final thermal performance of an application.
These factors include:
- The time of exposure to elevated temperature
- The rate of temperature increase
- The part geometry
The HDT measure for a specific polymer grade also depends on the base resin and the presence of reinforcing agents, fillers or plasticizers.
For instance, in the chart above, the homopolymer or copolymer of polypropylene has a HDT value range of 50-60 oC. Compare that value to the 30-40% glass-fiber reinforced grade of polypropylene, which is more than double the temperature (125-140 oC). A factor like this would influence the material choice for a designer wanting to use polypropylene for the end use product.
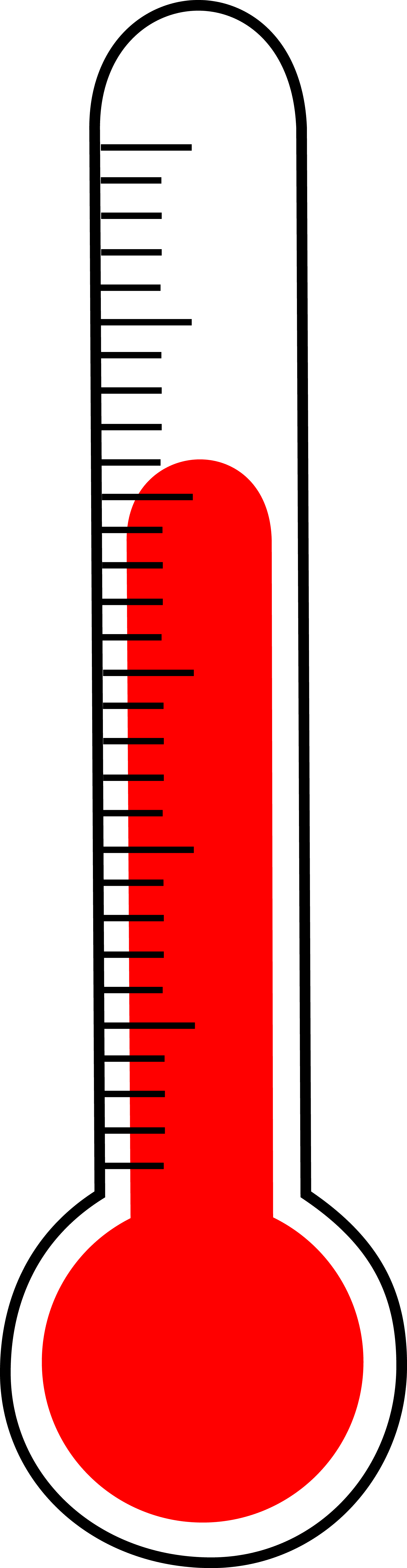
A combination of additives will always have a different effect on the HDT and the performance of a polymer overall.
- Reinforced and filled grades have a higher HDT (harder and stiffer under the heat)
- Plasticizers decrease HDT by making the polymer softer and more flexible
AIP: Unmatched Precision. Unrivaled Experience
Data charts can give you the heat deflection temperature, glass transition and other values. However, a chart can give a general idea of these values, but an entire data set with the curve of a material is the best way to determine the right material for your project.
Be sure to work with a plastics machining company that can provide you a wide range of data on the HDT and other values of polymers and composites. Your machinist will be able to give you a detailed response on how the heat deflection temperature will affect your project’s design and functionality. Talk to one our engineers at AIP about your project design, and we will work with you to provide unrivaled expertise from your project’s initial concept to completion.
Supporting Materials
Certifications and Technical Data Resources
Learn more about the material properties we consider when
working on a precision plastics machining project.