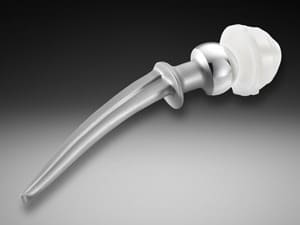
Source: Plastics Today
Ultra-high molecular weight polyethylene (UHMWPE) is part of the umbrella of polyethylene thermoplastics. Other peers include low-density polyethylene (LDPE) and high-density polyethylene (HDPE). Although UHMWPE embodies many similar qualities as HDPE, it is much stronger and carries a significantly higher resistance to chemicals, wet environments and withstands abrasion 15 times greater than carbon steel. This is why, among its many applications, it is the most common material for total joint replacements.
AIP has over 37 years of experience machining complex components from thermoplastics like ultra-high molecular weight polyethylene. In this insightful technical brief, we will discuss what goes into machining UHMWPE and how it differs from other manufacturing options such as metal machining, injection molding, and 3D printing.
Properties of UHMWPE
Keeping information about the properties of a thermoplastic beforehand is always beneficial. This helps in selecting the right thermoplastic for a project. Furthermore, it assists in evaluating if the end use requirement would be fulfilled or not. Here are some of the key properties of ultra-high molecular polyethylene:
UHMWPE is a part of the family of polyethylene thermoplastics. One of its defining characteristics is its toughness and high impact strength; this is due to long polymer chains with a molecular mass between 3.5 and 7.5 million amu. With a long chain, it has great bearing load which strengthens the intermolecular interactions. The result is a tough material that withstands incredible impacts and extreme temperature fluctuations.
Properties | Value | Units | Method |
Resistance to Weathering | Excellent | – | – |
Tensile Strength at Break | 24 | MPA | ASTM D638 |
Elongation at Break | 300 | % | Elongation at Break |
Thermal Expansion | 20 | 10-4K | ASTM D696 |
Coefficient of Friction P = 0.05 N/m2, v = 0.6m/s | 0.29 | – | – |
Impact Strength | No break | kJ/m2 | ASTM D256 |
Compressive Stress at 10% Deformation | 3,000 psi | PSI | ASTM 695 |
Dielectric Strength | 44 | kV.mm | ISO 60243-1 |
Melting Point | 130 – 136 266 – 277 |
C F |
– |
Service Temperature | Short term.120 Long term. 90 |
C | – |
Flammability | HB | – | UL94 |
- Low moisture absorption
- Chemical resistant
- High thermal conductivity
- Low dielectric constant
- FDA compliant
- Low coefficient of friction
- Self-lubricating
- Resistant to UV radiation
Applications of UHMWPE
Common applications for UHMWPE include: food processing equipment, water treatment, conveyor lines, wear strips, bearings, gears, pistons, valves, marine equipment and wet environments that require harsh cleaning. Let us take a closer look at some of the major applications of this mighty material.
Fiber
UHMWPE as a fiber is branded under the name Dyneema and Spectra. They have yield strengths as high as 2.4 GPa (2.4 kN/mm2 or 350,000 psi) and density as low as 0.97 g/cm3. High-strength steels have comparable yield strengths, and low-carbon steels have yield strengths much lower (around 0.5 GPa). Dyneema and Spectra have a strength-to-weight ratio eight times that of high-strength steels.
This fact makes UHMWPE a top-pick for industries requiring heavy-duty protection and strength from a fiber. Applications include personal armor and vehicle armor for military and defense industries.
Civil applications containing UHMWPE fibers are cut-resistant gloves, bow strings, climbing equipment, automotive winching, fishing line, spear lines for spearguns, high-performance sails, suspension lines on sport parachutes and paragliders and yacht rigging.
Medical
Since the 1960s, UHMWPE has also been the biomaterial of choice for total joint arthroplasty in orthopedic and spine implants. Clinical studies continue to work to improve its effectiveness for hip, knee and spine implants.
In 1998 one advancement introduced highly cross-linked UHMWPE. These new materials are cross-linked with gamma or electron beam radiation (50-105 kGy) and then thermally processed to improve their oxidation resistance. They have since become the standard of care for total hip replacements.
As of 2007, clinicians started incorporating anti-oxidants into UHMWPE for hip and knee arthroplasty bearing surfaces. The anti-oxidant improves oxidation resistance to the UHMWPE without the need for thermal treatment.
Marine
UHMWPE is a polymer that retains its properties in extreme environments, such as the marine industry. It is often used in marine structures and vessels for the mooring. UHMWPE forms the contact surface between the floating vessel and the fixed one. UHMWPE is chosen as the facing of fender systems for berthing structures because of the following properties: wear resistance, impact resistance and low friction (wet and dry conditions).
Grades of UHMWPE
At AIP, we machine various grades and brand name ultra-high molecular weight polyethylene. Branded names include the following: TIVAR®, POLYSTONE® M, LENNITE®, HOSTALEN GUR®, UHMW-PE, CERAM P, ULTRAPOLY CL6, ULTRAPOLY W1.
Our close ties with the industry’s leading plastics manufacturers give us even further insight and access to technical help in material selection, sizing and manufacturing procedures. Whatever your application, our machinists can help you in material selection, sizing and manufacturing techniques from concept to completion.
Machining UHMWPE
Annealing UHMWPE
Thermoplastics are prone to stress cracking and premature part failure when placed under high heat and tensile load. Therefore, annealing is crucial if you want a quality, precision machined part out of the stock shape. The annealing process at AIP greatly reduces the chances of these stresses occurring from the heat generated during machining UHMWPE and other polymers. Our machinists use computer controlled annealing ovens for the highest quality precision machining.
Generally, UHMWPE should be heated between 135 C to 138 C in an oven or liquid bath of silicone oil or glycerine. It is then cooled down at a rate of 5 C/hour to at least 65 C. Afterwards, it should be wrapped in an insulating blanket for 24 hours to bring to room temperature.
Machining UHMWPE
We recommend non-aromatic, water-soluble coolants because they are most suitable for ideal surface finishes and close tolerances. These include pressurized air and spray mists. Coolants have the additional benefit of extending tool life as well.
Some companies machine both metals and plastics, which has detrimental outcomes for machined polymer products. Many past experiences have shown parts going to customer without cracks, only to develop surface cracks and warping over time due to exposure to metal machine shop fluids. Be sure to use a facility like AIP that only machines polymers.
Preventing Contamination
Contamination is a serious concern when machining polymer components for technically demanding industries such as aerospace and medical sciences. To ensure the highest level of sanitation down to the sub-molecular level, AIP Precision Machining designs, heat-treats, and machines only plastics with any sub-manufactured metalwork processed outside our facility. This allows us to de-risk the process from metallic cross contamination.
Ultra-high Molecular Weight Polyethylene Machining Guide: Supportive Information
Quality Assurance Certifications
UHMWPE is one of several thermoplastics we machine for the medical and life sciences sector.
Learn about 8 other common thermoplastics and their medical applications.