An Informational Brief on Polymer Machining
Most people recognize Polymethyl methacrylate (PMMA) under the household name “acrylic.” This performance polymer is best known as a shatter-proof alternative to glass. Where transparency, UV stability, colorability and surface hardness are concerned, PMMA is a safe, cost-efficient option. It has good scratch resistance compared to other transparent polymers like Polycarbonate and can be coated with special abrasion and chemically resistant coatings to improve scratch and chemical resistance. For this reason, it has several applications across a variety of industries, including healthcare, specialized industrial, and aerospace and defense.
AIP has over 38 years of experience machining complex components from thermoplastics like Polymethyl methacrylate (PMMA). In this insightful technical brief, we will discuss what goes into machining PMMA and how it differs from other manufacturing options such as metal machining, injection molding, and 3D printing.

Properties of PMMA
Plastics machinists should keep data on the properties of the thermoplastics they use. Keeping a catalogue of data on thermoplastics used helps immensely during the material selection process. Additionally, it helps determine if the material is a good candidate for the end-use. Following are some of the key properties of Polymethyl methacrylate, acrylic (PMMA):
Key Properties
- Chemical resistance
- Durability
- Tensile strength
- Lightweight
- UV Stability
- Transparency
- Colorable
Description
PMMA, polymethyl methacrylate, commonly known as acrylic, is produced from the monomer methyl methacrylate. This thermoplastic is completely amorphous. It is often used as a shatter-proof replacement for glass, due to its excellent transparency, durability and UV stability.
PMMA comes in the form of clear, colorless pellets, granules and sheets. These can be machined with the following thermoplastic methods: injection molding, compression molding and extrusion. It is a stronger material than molding grades due to its high molecular mass. Rubber additives are used to increase PMMA’s toughness, since it can be brittle under heavy loads. An added plus of PMMA is it’s 100% recyclable.
As with many polymers, pure PMMA does have limitations that hinder it from usage in certain applications. In such cases, additives, fillers and co-monomers help to improve PMMA’s characteristics for better impact resistance, chemical resistance, flame retardancy, light diffusion, etc.
The table below displays an overview of the material properties, units and values for machining PMMA, acrylic:
Material Property | Units | Value |
Tensile Elongation at Break @73 F | % | – |
Flexural Modulus of Elasticity @ 73 F | psi | – |
Tensile Modulus of Elasticity @ 73 F | psi | 470000 |
Flexural Strength @ 73 F | psi | 14200 |
Specific Gravity @73 F | ASTM D792 | 1.19 |
Tensile Strength @73 F, (ult)/(yld) | psi | 8800 (ult) |
Notched Izod Impact @73 F | ft-lb/in of notch | 0.4 |
Heat Deflection Temperature @ 264 psi | F | 165 |
Flammability Rating | UL94 | – |
Coefficient of Linear Thermal Expansion @73 F | in/in/F | 4.0E-05 |
Dielectric Strength, Short Term | Volts/mil | 500 |
Water Absorption, Immersion, 24 hours Water Absorption, Saturation |
% by weight % by weight |
– 0.03 |
Applications of PMMA
From biotechnology to structural elements in buildings, PMMA is a versatile thermoplastic material. It is most commonly used as a substitute for glass in the signage industry, since it is shatterproof, cost effective and lightweight. Its applications in place of glass are endless, including: skylights, bulletproof glass, riot shields, , paneling for aquariums and large stadiums where light and translucent construction are critical.
Acrylic is commonly used in layer fluidic manifolds so that equipment operators can visualize the flow paths. Some manifold companies possess special processes to manufacture multi layered diffusion bonded PMMA manifolds. Methacrylate polymers are used extensively in dental and medical applications where purity and stability are critical to performance.
Common Applications
- Lenses for glasses
- Skylights
- Building barriers
- Bulletproof glass
- Exterior lights on vehicles
- Intraocular implants
- Bone cement in orthopedic surgery
- Acrylic prosthetics and artificial teeth
- Various artistic and aesthetic applications
AIP Machining Capabilities: Unrivaled Expertise
Our close ties with the industry’s leading plastics manufacturers give us even further insight and access to technical help in material selection, sizing and manufacturing procedures. Whether you are looking for a trademarked material or a specific polymer blend, we store an array of material bases at our machine shop for expert machining. Our machinists bring decades of experience to their craft and are prepared to help you in material selection, sizing and manufacturing techniques. From concept to completion, we work with you every step of the way to bring you a finished precision project.
Our Suppliers
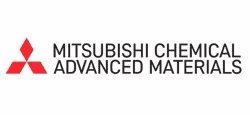
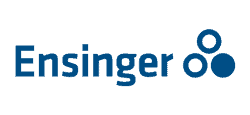
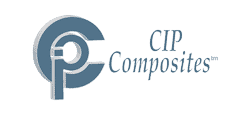
Machining ABS
Annealing ABS
As with any CNC machined part, annealing and stress-relieving is imperative to the machining process. Coolants, lubricants and trained procedures prevent cracking and crazing in a precision machined component. This is especially true with PMMA parts. Without proper stress relieving procedures, precision acrylic parts are prone to delayed crazing and stress cracking. Sometimes months after shipment. We recommend slow heating and cooling during the annealing process of a chosen thermoplastic. This reduces the chances of stresses occurring from the heat generated during machining polymers like PMMA. Our AIP machinists use computer controlled annealing ovens for the highest quality precision temperatures and time control.
Machining ABS
In the case of extruding and precision CNC machining, your machinist will use machine grade PMMA. Extrusion temperatures for PMMA range from 180-250°C. A degassing screw with an L/D ratio of 20-30 is recommended. For the best results, use sharp tools, avoid excessive clamping and cutting forces and use coolants to prevent overheating. On the shop floor, we use non-aromatic, water-soluble coolants because they are most suitable for ideal surface finishes and close tolerances. These include pressurized air and spray mists. Coolants also extend tool life.
Machining Acyrlic is more difficult than first envisioned as it is a rather brittle and stress sensitive material. Not to mention most machine coolants and lubricants will attack the material in a time delayed manner (meaning all will seem well, but the chemicals are at work and the failure is often delayed). For mission critical components, it is best to leave the PMMA machining to a shop who is keenly experienced machining the material.
PMMA has excellent dimensional stability and transparency when compared to glass. On the negative side, acrylic has low impact strength and tends to be brittle in nature.
Some companies machine both metals and plastics, which has detrimental outcomes for machined polymer products. Many past experiences have shown parts going to customer without cracks, only to develop surface cracks and warping over time due to exposure to metal machine shop fluids. Be sure to use a facility like AIP that only machines polymers.
Preventing Contamination
Contamination is a serious concern when machining polymer components for technically demanding industries such as aerospace and medical sciences. To ensure the highest level of sanitation down to the sub-molecular level, AIP Precision Machining designs, heat-treats, and machines only plastics with any sub-manufactured metalwork processed outside our facility. This allows us to de-risk the process from metallic cross contamination.
ABS Machining Guide: Supportive Information
Quality Assurance Certifications
Miscellaneous Materials
Looking for more machining tips on performance amorphous polymers like TORLON?