Most polymers have a natural tendency to absorb water. In fact, some superabsorbent polymers are highly sought after in advanced applications for medical, construction and more. Yet, moisture absorption of thermoplastics leads to changes with regard to processing and properties.
It is crucial for machinists and designers to understand the moisture absorption of thermoplastics for CNC machining. During the design phase, this not only helps with initial material selection, but plays a role in predicting the life span of a part. At AIP, we take great care in providing unrivaled results to ensure the optimal dimensions and properties for machined polymers and composites. Join us in this technical brief as we give an in-depth explanation of the effects of moisture absorption for machined polymers.
Plastics Machining and the Importance of Water Absorption
Moisture / water absorption is the capacity of a plastic or a polymer to absorb moisture from its environment. Absorbed moisture sometimes acts as a plasticizer, reducing the glass transition temperature and strength of plastic (this is a reversible side effect). However, absorbed water also can lead to irreversible degradation of the polymer structure.
Some effects include:
- Dimensional and mass changes (swelling) caused by water absorption
- Extraction of water-soluble components
- Changes in mechanical (elasticity, tensile strength, impact strength) and electrical performance
Water absorption is expressed as increase in weight percent or % weight gain of a plastic specimen under the following testing procedures:
- Water Absorption 24 hrs at 23°C – Immersion of a plastic specimen in distilled water during 24 hours at 23°C
- Water Absorption 24 hrs at 100°C– Immersion of a plastic specimen in distilled boiling water during 24 hours Water Absorption at saturation – Immersion of a plastic specimen in distilled water at 23°C. Measurement occurs when the polymer does not absorb water anymore
- Water Absorption at Equilibrium– Plastic specimen is exposed to a humid environment — generally at 50% relative humidity — at a specified temperature — 23°C or 73.4°F — for 24 hours

(Source: Omnexus)
Exposure to humidity, immersion and boiling water can result in different material responses. The equilibrium moisture content can be used to compare the amount of water absorbed by different types of plastics when they are exposed to moisture.
Plastics Processing and Properties
Polymers are affected by moisture from their environment or from simply sitting on a shelf waiting to be used. This is not a huge concern, but when the moisture absorption reaches more than 1% or 2%+, this can result in enough dimensional movement to create concerns.
Moisture Absorption Affects:
- Mechanical properties
- Wear properties
- Dimensions
For example, parts made from TORLON (PAI) require special attention due to a 1.7% moisture at saturation value. While this number may not sound like much, it is enough to cause a precision machined TORLON part to exceed tolerance; in this scenario, the part cannot be used.
Therefore, it is important to properly package these mission critical polymers for lasting shelf-life and function. This can be achieved in two ways: 1) Vacuum-sealing them in a moisture-impermeable layer or 2) packaging them with bags of desiccant. This prevents moisture uptake in humid environments.
Tests to Measure Water Absorption of Plastics
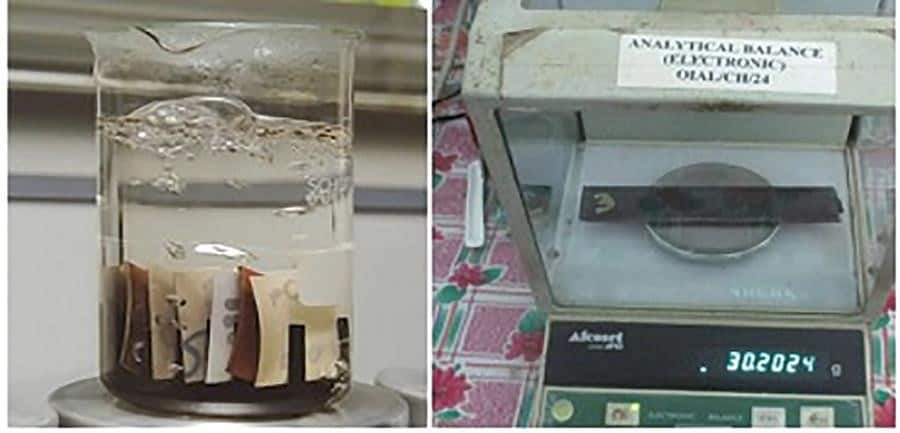
ASTM D570 – Standard Test Method for Water Absorption of Plastics
This test method for rate of water absorption has two main functions:
- A guide to the proportion of water absorbed by a material and consequently, in those cases where the relationships between moisture and electrical or mechanical properties, dimensions, or appearance have been determined, as a guide to the effects of exposure to water or humid conditions on such properties.
- A control test on the uniformity of a product. It is particularly applicable to sheet, rod, and tube arms when the test is made on the finished product.
Procedure: Parts are dried in an oven for a specified time and temperature and then placed in a desiccator to cool. Upon cooling, the specimens are weighed to establish a point of reference. The material is then submerged in water at standardized conditions (usually 23°C for 24 hours or until equilibrium). Specimens are removed from the liquid, dried and weighed.
What affects water absorption?
- Type of plastic
- Morphology (crystalline, amorphous…)
- Type and proportion of additives, fillers and reinforcements used
- Fiber fraction and orientation (in composites)
- Relative humidity and temperature
- Length of exposure
Water Absorption Values for Common Polymers
Polymer Name | Min Value (% weight) | Max Value (% weight) |
ABS – Acrylonitrile butadiene styrene | 0.05 | 1.80 |
PA – Nylon Polyamide, 66 30% Glass Fiber | 0.80 | 1.10 |
PAI – Polyamide-Imides (TORLON) | 0.10 | 0.30 |
PBI – Polybenzimidazole (CELAZOLE) | 0.4 | 5 |
PC – Polycarbonate, high heat | 0.10 | 0.20 |
PE – Polyethylene, 30% glass fiber | 0.02 | 0.06 |
PEEK – Polyetheretherketone | 0.10 | 0.50 |
PEI – Polyetherimide (ULTEM) | 0.20 | 0.30 |
PP – Polypropylene | 0.01 | 0.10 |
PS – Polystyrene, high heat | 0.01 | 0.07 |
PSU – Polysulfone | 0.20 | 0.80 |
PTFE – Polytetrafluorethylene | 0.005 | 0.015 |
PVC – Polyvinyl chloride, rigid | 0.04 | 0.40 |
PVDF – Polyvinylidene fluoride (KYNAR) | 0.03 | 0.05 |
As the chart notes, some polymers such as Nylon (PA) have a higher rate of % gain from moisture absorption. However, polymers like PVDF and PTFE have a very low % gain in weight after the ASTM D570 test – which makes them excellent candidates for applications where moisture is a factor.
Performance thermoplastics are often exposed to high temperature applications (aircraft engines) which also absorb high levels of moisture. This is common in materials such as PBI (Celazole) and PAI (Torlon), since these polymers absorb moisture at high rates but are also specified in high temperature applications.
Basically, what can happen is that these materials absorb the moisture if not properly stored and packaged. Then if subject to high levels of heat without time for the moisture to dissipate, the internal moisture boils and turns to steam causing the parts to crack and blister.
Managing Moisture Absorption
For predictable machined part fit and performance, stock shapes and finished parts should be stored in a dry environment. Both finished parts and stock shapes should be packed in moisture barrier packaging. Only open packaging just prior to use. In the event that a part may have adsorbed so much moisture as to risk shocking it when placing it in high temperature or vacuum service, consider drying the material prior to use or re-use.
Your machining facility will have specifications on temperature and storage procedures for all polymers, stock shapes and components. When it comes to critical applications, work with a machine shop that has high standards for storing products. After all, machining a polymer is only part of the entire process; wasted machining, revenue and parts is not worth risking poor storage conditions. The table below shows some common packaging for polymers to increase and preserve shelf-life.
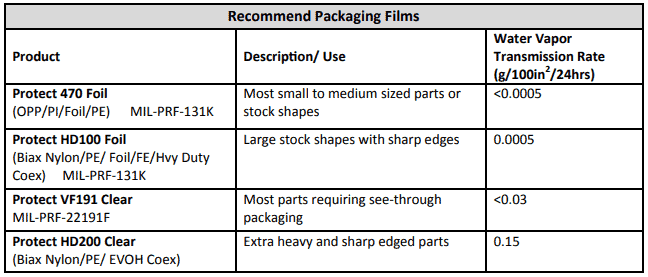
Generally, you can find a polymer’s 24 Hour and Saturation Moisture Absorption Values on a data chart. A chart can give a general idea of the moisture absorption, but an entire data set with the curve of a material is the best way to determine the right material for your project. Be sure to work with a plastics machining company that can provide you a wide range of data on the moisture absorption of polymers and composites. Your machinist will be able to identify how moisture and humidity will affect your project’s design and functionality. Talk to one our engineers at AIP about your project design, and we will work with you to provide unrivaled expertise from your project’s initial concept to completion.
Supporting Materials
Certifications and Regulatory Resources