Your Brief Guide to Polymer Materials
When it comes to polymers, you have two basic types: thermoplastics and thermosets. When machining plastic, it’s crucial to know which one you’re working with due to distinct differences between how these two main polymer categories react to chemicals and temperature.
Thermoplastics soften when heated and become more fluid as additional heat is applied. The curing process is completely reversible as no chemical bonding takes place. This characteristic allows thermoplastics to be remolded and recycled without negatively affecting the material’s physical properties.
Thermoplastics possess the following properties:
- • Good Resistance to Creep
- • Soluble in Certain Solvents
- • Swell in Presence of Certain Solvents
- • Allows for Plastic Deformation when Heated
Thermosets contain polymers that cross-link together during the curing process to form an irreversible chemical bond. The cross-linking process eliminates the risk of the product re-melting when heat is applied, making thermosets ideal for high-heat applications such as electronics and appliances.
Thermosets possess the following properties:
- • High Resistance to Creep
- • Cannot Melt
- • Insoluble
- • Rarely Swell in Presence of Solvents
Phenolic, Bakelite, Vinyl Ester and Epoxy materials would be considered examples of a thermoset, while ULTEM, PEEK, TORLON and Polycarbonate materials are examples of thermoplastics.
The thermoplastic category of polymers is further categorized into Amorphous and Crystalline polymers per the figure below:
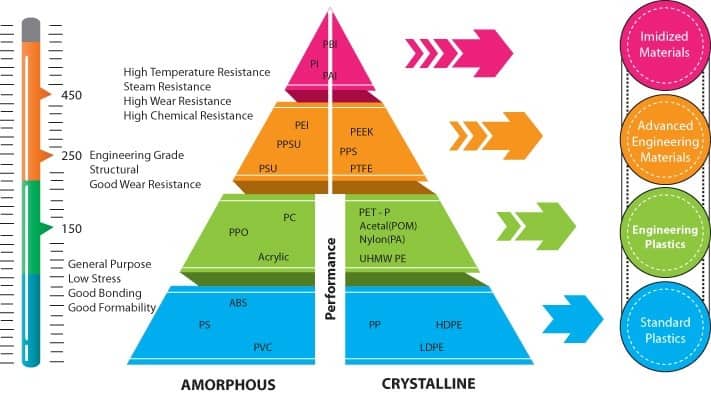
Most amorphous polymers are thermoform capable, translucent and easily bonded with adhesives or solvents. One example of this would be TORLON.
Semi-crystalline polymers are difficult to bond or thermoform, but possess better chemical resistances, electrical properties and a low coefficient of fiction. An example of a semi-crystalline polymer would be PEEK.
Want to learn more about AIP’s polymer and composite materials?
or request a quote here.